I was looking to protect the underbody of a mini-bus which suffered from the projection and impacts of gravel which made the paint jump and flake (since tarring is prohibited in my corner: we have to paint ...) and each time it was necessary to reprocess and repaint ...
In short it was cumbersome to manage, especially since today's body paints are not really easy to apply, it becomes a specialized profession with water-based polymer paints, but primer with solvents, in short ... You have to work quickly, at the right temperature, something that you rarely have the opportunity to find outside now, or you have to wait for the summer ... In short, it's more like before .. .
Furthermore, neither the conventional 3M type anti-gravel, nor the tar offered a satisfactory solution, since when the rust progresses underneath, we only see it when it is already much too late to intervene and it sheets must be re-welded to replace the bodywork affected by corrosion. And it costs bomb ..
I pass on the details of the painting phase (just know that I found a great epoxy primer, for those who are interested ... but difficult to apply and you must carefully clean the gun afterwards, because obviously, it is epoxy so hereto glue!! The advantage is that we can use a thin layer, which means that we quickly see the rust starting underneath, just in case ... And we can finally intervene very early!)
Misuse of PU (polyurethane) foam
First of all, one might be surprised by such a choice which seems at first sight not very ecological. Only here, doing the paint work on the rocker panels also involves pollution by fumes of solvent vapors, and that's really bad ... And for your lungs and for the atmosphere. Anyway, in the end, I considered that it was the least harm ... This especially as running a compressor and power tools to remove corrosion and paint, also has its energy cost, so one in the 'other...
We find this PU foam in different forms:
To coat and insulate plumbing pipes ... As here:

Or as a floor mat, for campers or fitness ... Like this:

I planned to put hoops and also use the existing hooking points under the chassis to hold my foam, but I did not need it, here is why:
So I bought 4 floor mats for campers:
... I chose those that come in two layers: one side resistant to humidity (necessarily turned to the side of the road) and the other for comfort insulation.
Then - after making a pattern - I traced the cutting areas (with a good margin of at least 7cm all around, to do with the type of foam, because it compresses more or less ...):

... then my idea was to make a collage or to hold it thanks to hoops that I had started to cut ...
It was then that I had the idea of using a glue. So I asked our chemist if he had an idea of the type of glue they used to join the two layers of this PU foam mat. It was there that he told me that they did not use glue at all, but a grille and did it hot! Eureka, my blood only went around, so I just had to determine the ideal temperature and find the way to heat and assemble with the simplest method ...
So I tested with an electric plate on which I heated a cutter blade:

We arrive quickly enough to find the right temperature, it just has to melt a little ...! What is amazing is the strength with which it holds. Once cooled, pull it a little until it breaks, but it will not give way at the place of the weld, but next to it! (Test with yours of course, it must depend on the material too, you can never be careful enough). You also need a breathing tube, which will take fresh air a little further ... it may be better not to breathe too much ...
Then we had to develop the right working method ...!
- Prepare the area to be bonded already in its final place under the vehicle chassis;
- Approach the electric plate as close as possible and heat the very hot cutter blade;

- Present it at high temperature in the area to be welded (be careful not to get burned!);
- then press the two parts to be joined against the blade simultaneously:

- Then at the second when it has melted, simultaneously on both sides to be assembled: immediately remove the blade and assemble the two parts, holding them together by exerting sustained pressure against each other for 20 to 30 seconds (i.e. depending on the type of PU foam ...):

Once finished, you just had to cut out the "stairs" that remained between the different parts assembled with a chisel, and it made two beautiful shells, easy to remove or replace:

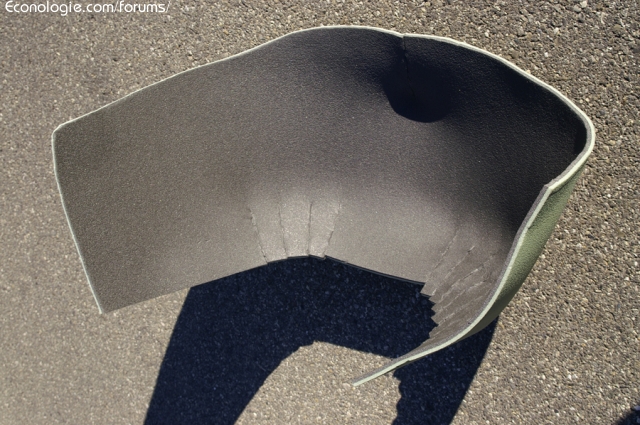
Advantages, it is very light (probably lighter than the thick anti-gravel, so no additional fuel cost), it is cheap (from 6 € each at Lidl) and easy to implement ... It there is no risk of the fact that even if it were to tear it is very soft, so it is not of consequence (but we will take care to put it in place with care, with hooking areas of large washers in plastic (I cut large rounds of flexible plastic from liquid detergent stagnons, it's flexible, it's going very well, and it cost me nothing ...)
Other applications: in house insulation. So we can weld the insulating shells in PU foam or instead of leaving them open or badly glued with the tape supplied! The big advantage is that they can be adapted to the diameter of the pipe! Because we can now manufacture them to the diameter we want!